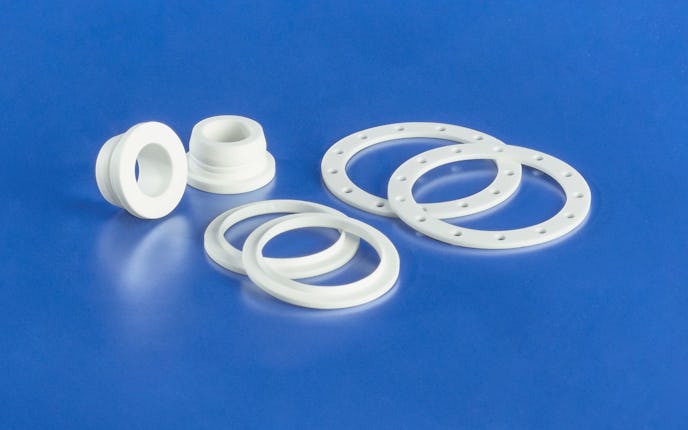
Our offering
- High-quality seals and moulded parts made of technical ceramics additively manufactured
- Advice on material
- Design & development
- Individual and complex geometries possible
- Production from aluminium oxide and zirconium oxide
- From quantity 1 up to series production
- High quality